Commercial construction often have stricter codes, larger budgets, and more complex approvals than residential projects. Each commercial construction project type serves a different function and comes with its own requirements. Knowing the differences helps you plan smarter, stay compliant, and manage risk from day one.
1. Restaurant Construction
Restaurant construction is one of the highest-turnover categories in commercial building, but that doesn’t mean it’s simple. Behind every polished dining room is a deeply coordinated build with strict compliance requirements, tight programs, and operations-focused design.
Key Features
- Specialized Kitchen Infrastructure: Commercial kitchens demand extensive MEP coordination. Expect high-capacity exhaust systems, fire suppression hoods, grease interceptors, and washable surfaces throughout. Kitchen design drives much of the back-of-house layout and impacts early-stage trades like plumbing and concrete.
- Front-of-House Ambience Meets Code: Dining areas need to hit brand standards while complying with fire safety, egress paths, ADA access, and occupant load requirements. Designers and contractors must work in tandem to preserve aesthetics without compromising compliance.
- High Regulatory Load: Health departments, fire marshals, building inspectors, and accessibility consultants all weigh in. It’s not uncommon for inspections to be phased (rough, hood-only, occupancy), which adds complexity to project scheduling.
- Condensed Timelines: Quick service restaurants (QSR) and franchises often operate on 8–12 week build programs. That leaves little room for procurement delays, change orders, or incomplete design documentation.
- Tenant Improvement + Ground-Up Models: Restaurant projects can range from minor retail conversions to full-scale pad site builds. Each project delivery method brings a different set of preconstruction needs, including site utilities, grease waste routing, slab penetrations, and AHJ coordination.
- Franchise Standardization: Chain restaurants typically provide base design packages and finish schedules, but they still require local adaptation. Construction teams must navigate both corporate review cycles and local permitting.
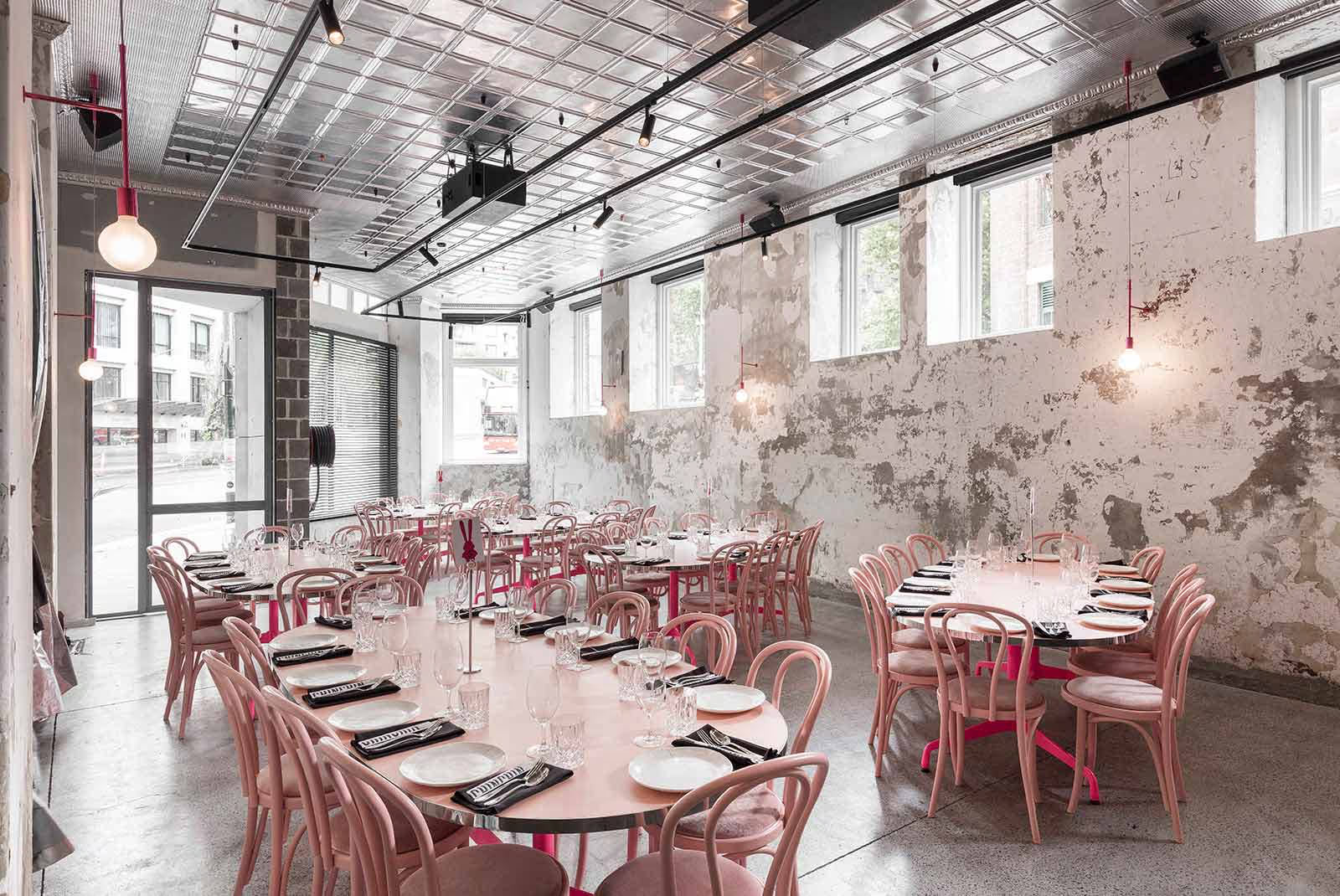
Example: Chin Chin Sydney (Lucas Restaurants)
This major fit-out in Surry Hills involved repurposing a heritage-listed site with a high-end kitchen, custom interiors, and strict compliance with fire and accessibility codes, all within a tight schedule to meet the restaurant’s high-profile launch.
2. Medical Facility Construction
Medical construction demands precision. These include hospitals, outpatient clinics, or specialty labs. These facilities must support critical operations, meet stringent codes, and allow zero tolerance for downtime or contamination. From electrical systems to finish selections, everything needs to serve a clinical function and comply with multiple regulatory layers.
Key Features
- Complex MEP Systems with Redundancy: Hospitals and medical buildings require layered power systems, including emergency backup (often via dedicated generators or UPS systems). HVAC design must account for pressure-controlled environments (positive for ORs, negative for isolation rooms), with HEPA filtration, humidity control, and zoning tied to infection control protocols.
- Healthcare-Specific Compliance Standards: Builds must align with FGI Guidelines, ADA, NFPA 99, and local licensing authority codes (e.g., Department of Health or Joint Commission). These standards govern everything from corridor widths to sink locations to wall types in patient areas.
- Equipment-First Design Philosophy: Imaging suites (MRI, CT, PET) and surgical theaters drive structural and MEP decisions from the outset. Shielding, slab penetrations, vibration control, and cooling loads all require early coordination with equipment vendors.
- Infection Control Measures: During construction or renovation of active facilities, ICRA (Infection Control Risk Assessment) protocols dictate containment, negative air pressure zones, daily cleaning, and strict routing of workers and materials. These controls must be factored into the schedule and budget.
- Patient-Centered Circulation and Access: ADA-compliant entryways, wide corridors, and low-resistance doors are standard. Beyond basic access, medical environments must prioritize workflow efficiency. This minimizes patient travel distances while enabling staff to move freely between departments.
- Design for Ongoing Adaptability: Medical technologies evolve fast. Mechanical systems, IT infrastructure, and room sizes must allow for future equipment retrofits. Flexibility in layout, ceiling systems, and access panels helps extend facility lifespan without major renovation.
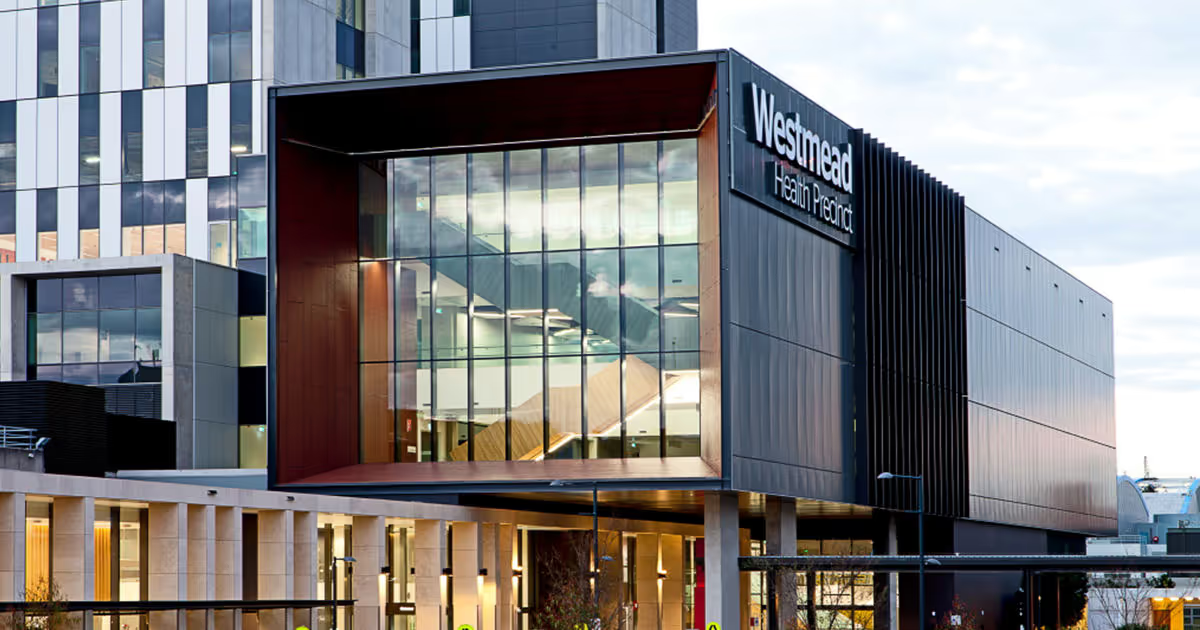
Example: Westmead Hospital Redevelopment (NSW)
A $1 billion+ upgrade involving new clinical services buildings, surgical suites, imaging centers, and helipads. The project demanded phased delivery, 24/7 operational continuity, and strict ICRA protocols due to work near active patient zones.
3. Hotel & Hospitality Construction
Hotels are multi-use facilities that function like small cities. From back-of-house logistics to high-end guest amenities, hotel construction requires detailed coordination across space types, finish levels, and building systems. Add in high guest turnover and 24/7 operations post-completion, and the pressure on the build quality multiplies.
Key Features
- Mixed-Use Programming Across Tiers: A single project may include guestrooms, suites, event halls, restaurants, spas, gyms, pools, retail areas, and back-of-house facilities. Each function carries its own structural, acoustic, MEP, and fire safety requirements. Coordination is critical to avoid scope overlaps and sequencing issues.
- Vertical Distribution Challenges: In mid- and high-rise hotels, careful attention must be paid to plumbing stacks, electrical risers, ductwork routing, and elevator cores. Staggered guestroom layouts require repeated detailing. But it must align precisely for MEP continuity.
- High-Touch Finishes and Mock-Up Requirements: Operators often demand detailed room mock-ups during early construction to approve finishes, lighting, millwork, and layout. These mock-ups serve as the standard for quality and become key reference points for trade coordination.
- Fire Life Safety and Egress Complexity: Hotels face stringent fire code enforcement due to overnight occupancy. This includes pressurized stairwells, smoke detection across zones, alarm override systems, and clear evacuation signage. Plus, coordination with local fire authorities for inspection sequencing is a must.
- Building Systems Must Support Guest Comfort: Noise transmission between rooms, air temperature fluctuations, lighting automation, and water pressure inconsistencies can impact guest satisfaction. MEP design must prioritize performance as much as efficiency.
- Operational Downtime Equals Lost Revenue: For renovations, phasing is everything. Construction teams often need to deliver floor-by-floor upgrades while keeping parts of the hotel open. Night work, quiet hours, and temporary systems become part of the logistics plan.
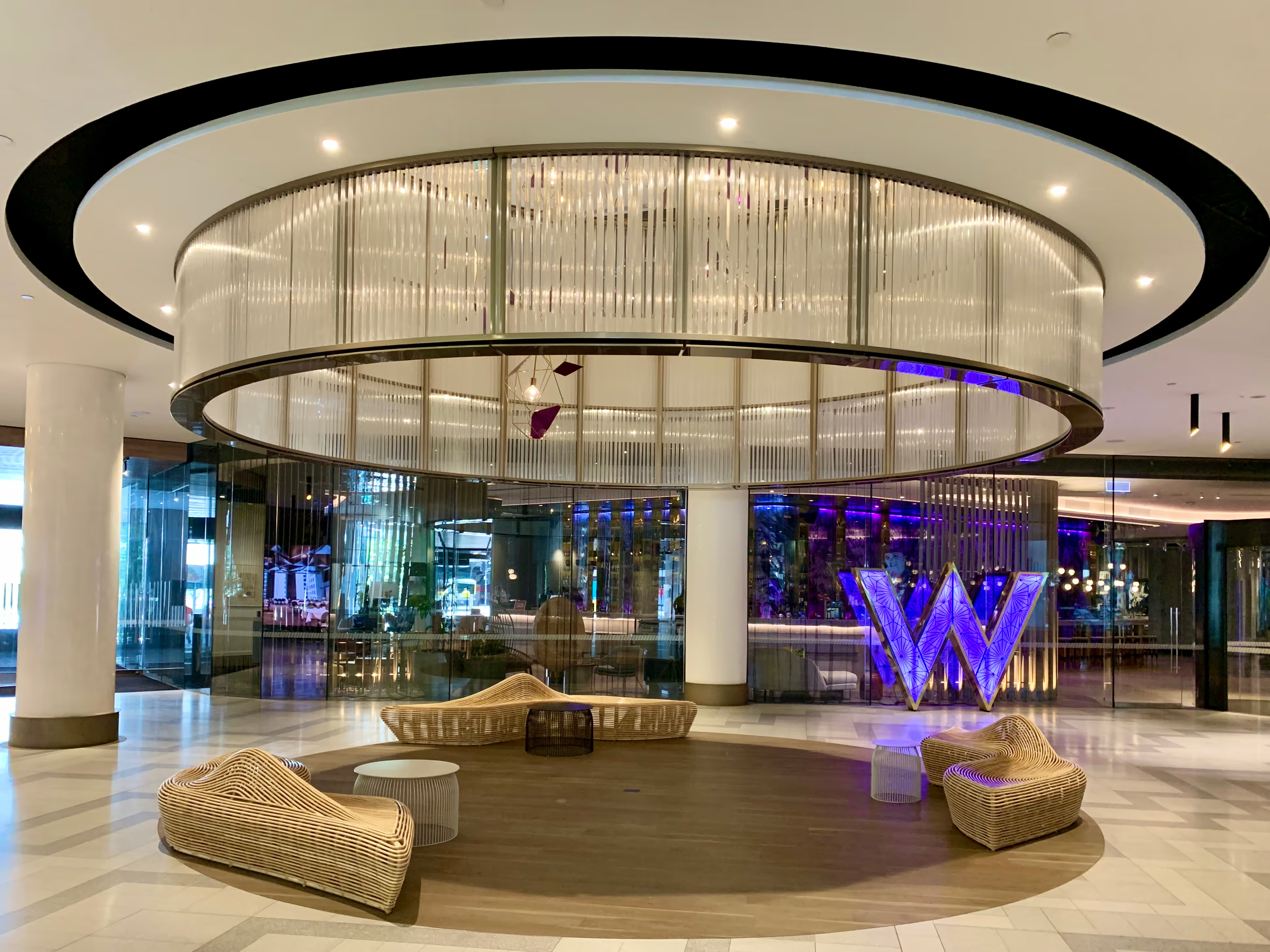
Example: W Hotel Brisbane
This 5-star riverside hotel includes 312 rooms, a rooftop bar, day spa, pool, and conference center. The build combined high-spec finishes, luxury amenities, and complex services integration across vertical floors in a CBD setting.
4. Office Building Construction
Office buildings used to follow a predictable model: core-and-shell structure, repetitive floor plates, and cookie-cutter tenant spaces. Not anymore. Modern office projects demand agile infrastructure, high-tech systems, and tenant-specific customization, all while hitting tight energy codes and ever-evolving workplace standards.
Key Features
- Core-and-Shell vs. Fit-Out Scope Split: Office projects are typically delivered in two major packages: base building (structure, envelope, vertical MEP) and tenant improvements (interior fit-outs, low-voltage, branding elements). Managing the interface between these two scopes is critical to avoid rework and coordination gaps.
- Integrated Technology Systems: Offices rely heavily on IT, AV, and access control systems. MEP coordination must accommodate server rooms, redundant fiber pathways, wireless access points, and smart lighting systems, especially in Class A developments.
- Amenity-Rich Programming: To attract and retain tenants, landlords are building more than just workspace. Think cafés, gyms, outdoor terraces, wellness rooms, and co-working hubs. Each of these spaces comes with its own MEP and acoustic challenges.
- MEP Load Planning Based on Occupancy Diversity: Open work areas, enclosed offices, and specialty zones (e.g., recording booths, podcast rooms) each require different airflows, lighting, and noise control. Mechanical zoning and electrical panel layouts must reflect this early.
- High Spec Finishes and Branding: Many office tenants want branded environments with polished concrete floors, custom millwork, and exposed ceilings. These architectural choices often introduce constructability challenges, like managing acoustics in open ceilings or hiding conduit within minimalistic designs.
- LEED, WELL, and ESG Drivers: More office buildings are pursuing green and wellness certifications. This affects everything from material procurement (low-VOC, FSC-certified) to daylighting, HVAC zoning, and water usage.
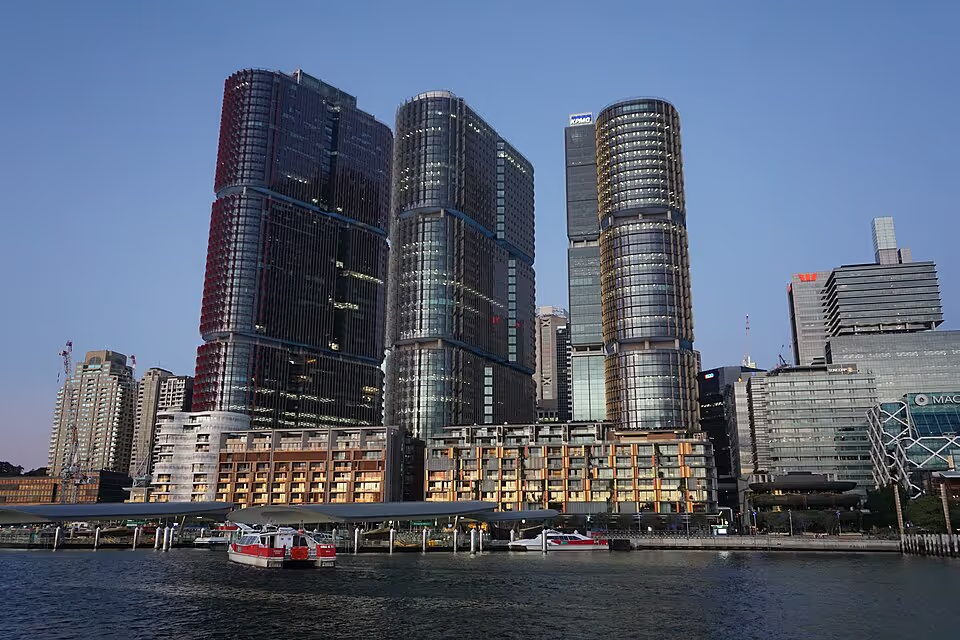
Example: International Towers Barangaroo (Sydney)
Part of the $6 billion Barangaroo South development, these towers feature cutting-edge workplace design, 6 Star Green Star ratings, advanced IT infrastructure, and tenant customization for companies like PwC and HSBC.
5. Retail Construction
Retail projects live and die by the customer experience. Whether it's a flagship store or a multi-tenant shopping center, construction must reflect brand identity, optimize layout for sales flow, and meet rigorous delivery schedules tied to grand openings.
Key Features
- Standardized Brand Design With Local Adaptation: National retail chains often supply construction drawings, finish schedules, and equipment specs. But even templated stores require local code adjustments, jurisdiction-specific permitting, and site-specific detailing (slab conditions, utility access, ADA paths).
- Fast-Track Delivery Model: Retail construction typically operates under aggressive timelines. This is often 60 to 90 days for tenant improvement, especially in mall or strip center environments. Fast decision-making, pre-bid coordination with vendors, and early material procurement are essential to meet launch dates.
- High-Footfall Design Considerations: Layouts must support intuitive circulation, clear sightlines, and easy access to merchandise. Finishes must withstand heavy wear and cleaning cycles. This includes polished concrete, LVT, and impact-resistant drywall are common.
- Shell + TI Coordination: Landlords usually deliver warm shells or grey shells, while tenants complete the interior. Precise handoffs between landlord and tenant scopes, e.g., sprinkler drops, HVAC distribution, electrical capacity, must be documented and enforced to prevent delays and scope gaps.
- Signage, Façade, and Brand Consistency: Exterior upgrades like branded signage, façade treatments, and storefront glazing often require additional permits or design reviews, especially in high-visibility locations or mixed-use developments.
- Utility and Service Needs Vary Widely: A grocery store may require refrigeration systems, backup power, and loading dock access, while a salon may need plumbing for every workstation. Construction must account for these functional differences in early layout and MEP design.
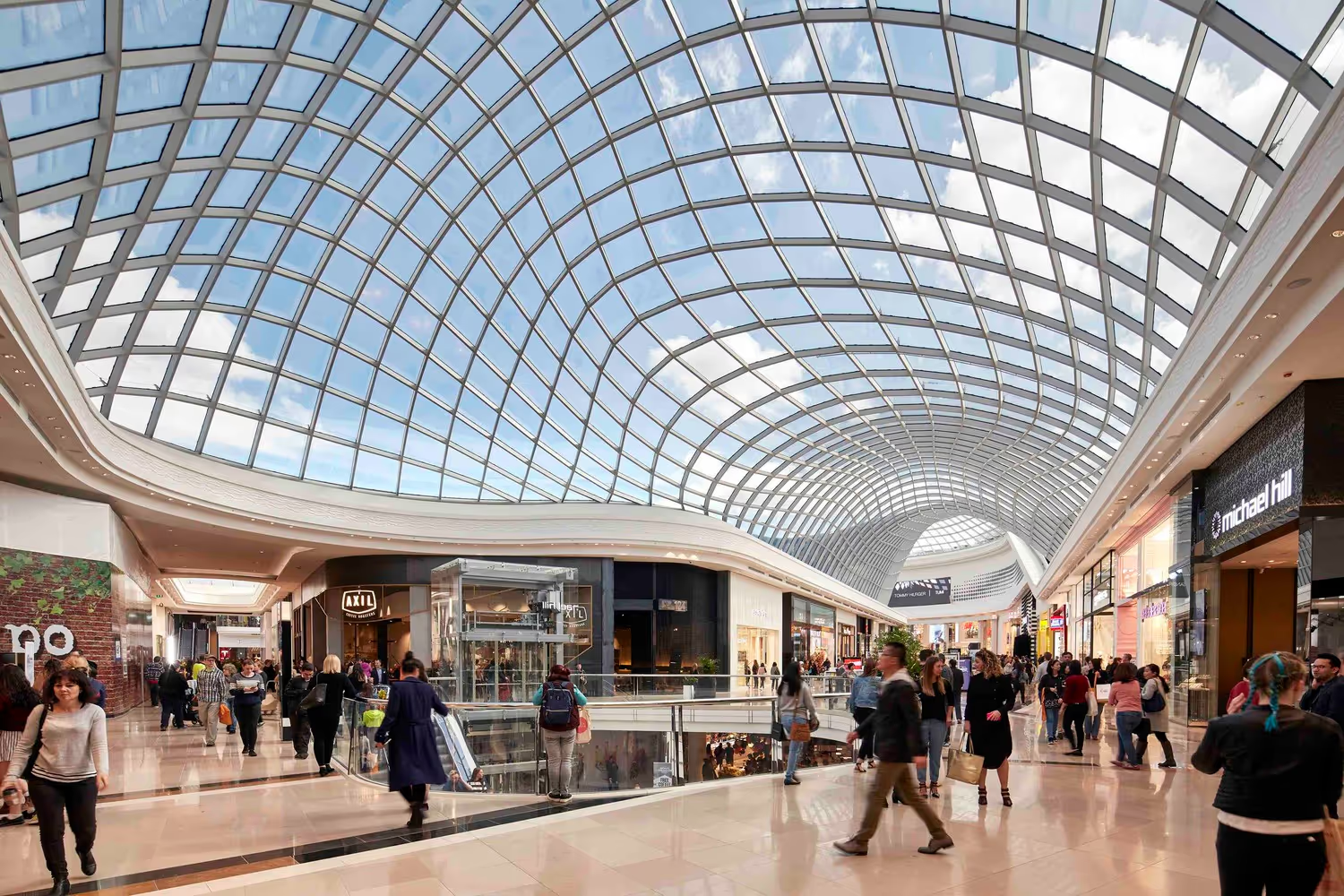
Example: Chadstone Shopping Centre Expansion (Melbourne)
Australia’s largest shopping center underwent a $660 million redevelopment to add luxury retail, new dining precincts, a hotel, and improved traffic flow. Complex staging allowed the center to remain operational throughout.
6. Sports & Recreational Facility Construction
Sports and fitness facilities are engineered for the movement of athletes, spectators, and support staff. Whether it’s a multi-sport stadium or a neighborhood fitness center, these builds demand durable materials, specialized layouts, and strict safety in design.
Key Features
- Purpose-Built Structural Systems: Gyms, courts, pools, and arenas often require long-span structures, vibration control, and high clearances. Truss systems, post-tensioned slabs, and reinforced foundations are common, especially for arenas with retractable seating or multi-court setups.
- Integrated AV and Broadcast Infrastructure: Professional and collegiate venues demand more than a scoreboard. Large-format LED displays, audio zones, fiber backbones, and broadcast booth connections must be embedded in the design from Day 1.
- Athlete and Spectator Segregation: Traffic flow design must separate player zones, loading docks, concessions, and audience paths. Safe crowd control and emergency egress are critical, often governed by NFPA 101 and local occupancy codes.
- High-Durability Interior Finishes: Floors, walls, and fixtures must withstand sweat, impact, equipment drag, and constant foot traffic. Common materials include seamless rubber flooring, resinous coatings, impact-resistant wallboard, and heavy-duty acoustic panels.
- Specialty MEP Requirements: Ventilation loads are high, especially in enclosed areas with intense physical activity. Pool facilities add corrosion concerns, while fitness spaces often demand spot cooling and energy recovery systems. Water, lighting, and HVAC must meet both energy codes and performance expectations.
- Flexible Programming and Multi-Use Layouts: Many facilities host a mix of events, from basketball and volleyball to trade shows and concerts. This requires operable partitions, retractable bleachers, and integrated power/data in slab and wall systems.
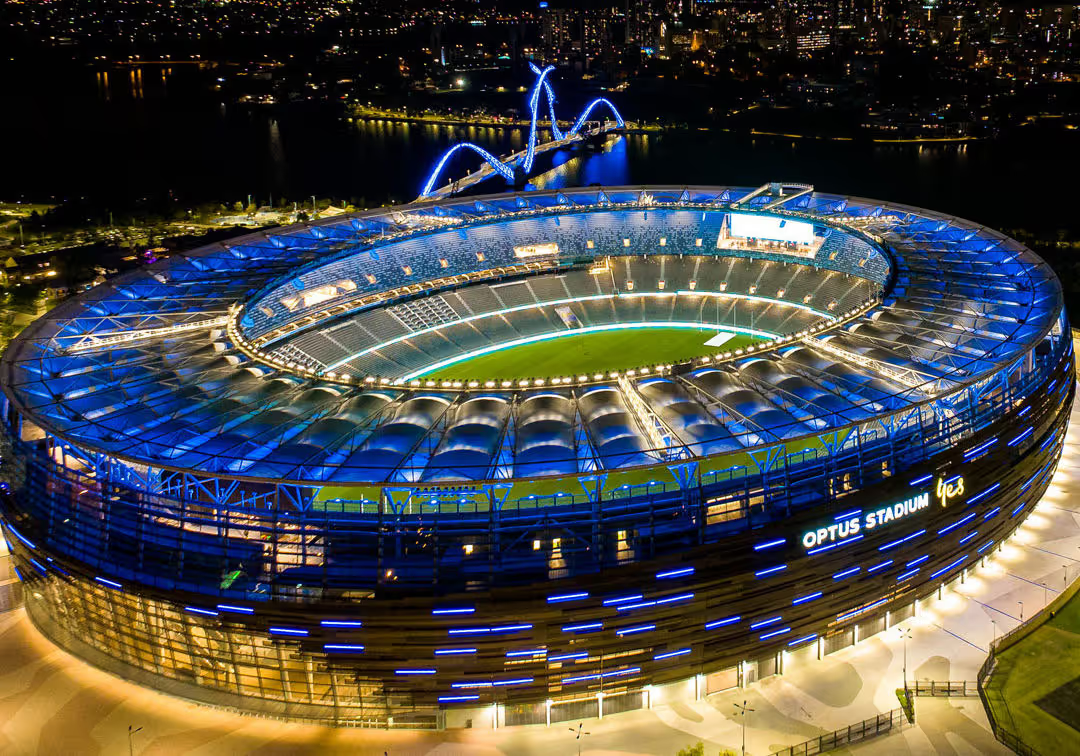
Example: Perth Stadium (Optus Stadium)
A 60,000-seat multi-purpose venue with retractable seating, high-tech AV, and integrated transport infrastructure. The project required extensive stakeholder consultation, Indigenous engagement, and precision crowd-flow modeling.
7. Institutional Construction
Institutional projects, like schools, universities, libraries, and civic centers, serve long-standing public functions. These are mission-critical spaces that must be safe, adaptable, and cost-efficient over decades of use. The planning is complex, the funding is often public, and stakeholder engagement doesn’t stop once shovels hit the ground.
Key Features
- Heavy User Load With Diverse Programming: Institutional buildings support dense, daily occupancy of students, staff, visitors, and administrators across a wide range of activities. This drives demand for robust infrastructure, clear circulation, and zoning by function (classrooms, admin, food service, sports, and residential).
- Design for Lifespan and Adaptability: These projects need 30–50+ year design life. That means using durable materials, standardizing room sizes for reconfiguration, and oversizing MEP systems to allow future load increases (e.g., data capacity, AV upgrades, lab retrofits).
- Code and Policy Driven: Public buildings are typically subject to local, state, and federal code overlays, including Department of Education guidelines, fire marshal input, environmental performance mandates (e.g., Green Star or LEED), and universal access rules.
- High-Volume AV and IT Requirements: Classrooms and lecture halls demand AV-first design: projector mounting points, cable pathways, acoustic modeling, and centralized control systems. Network closets and IDF rooms must be planned early and built to spec.
- Phased Construction or Occupied Renovation: Many institutional projects are built in active environments. That means temporary egress, noise isolation, infection control (in healthcare education), and aggressive scheduling around academic calendars.
- Public Engagement and Oversight: School boards, city councils, or university stakeholders often drive approval cycles. Construction teams must manage high transparency, public meetings, and regular reporting on progress, budget, and safety.
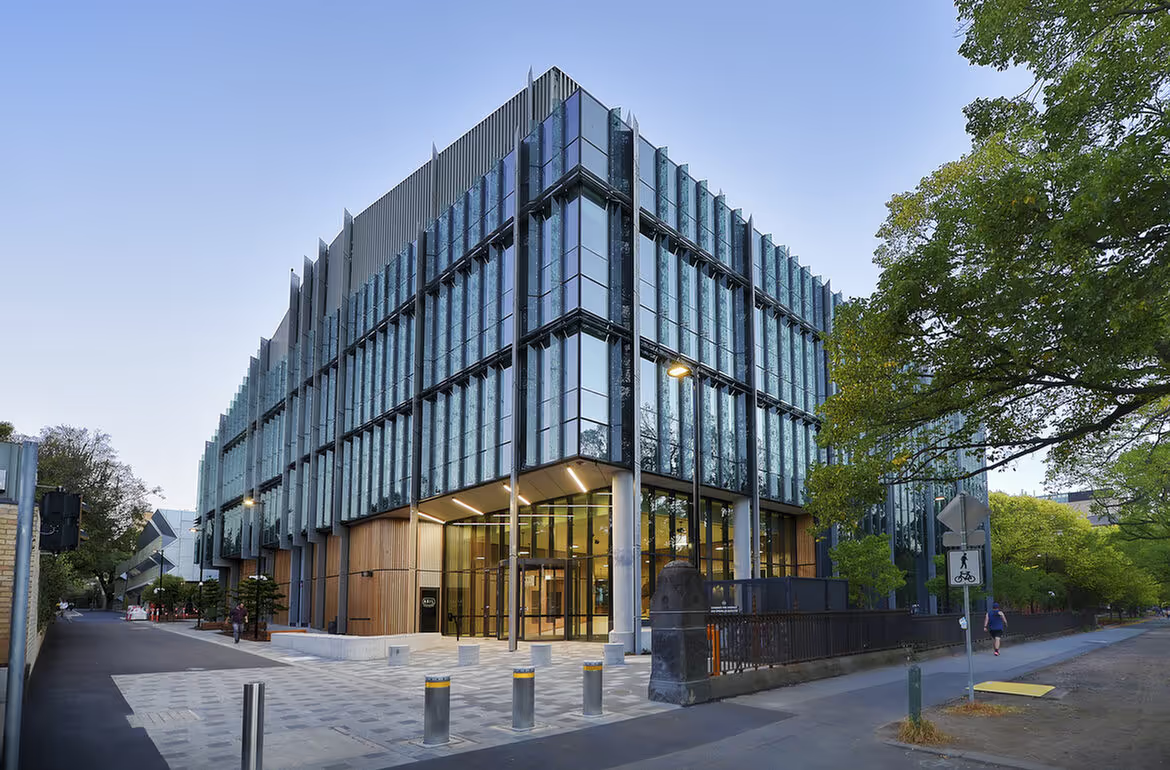
Example: University of Melbourne’s Western Edge Biosciences Project
A multidisciplinary research and teaching hub with PC2 labs, high-spec AV, active learning spaces, and sustainable design features. Delivered under a live campus environment with staged handovers to minimize disruption.
8. Industrial Construction
Industrial buildings are production engines. Whether it's a manufacturing plant, logistics hub, or cold storage warehouse, industrial construction is all about the flow of goods, equipment, vehicles, and energy. These are highly engineered spaces designed for uptime, safety, and efficiency, not aesthetics.
Key Features
- Large-Span, High-Clearance Structures: Industrial builds often feature wide-open bays, steel frames, and slab-on-grade foundations. High bay ceilings (28–40 ft+) and column-free layouts maximize storage density and equipment maneuverability. Load-bearing and slab design must accommodate heavy racking, forklifts, and point loads from machinery.
- Specialized Mechanical and Process Systems: Depending on the facility type, systems may include dust collection, compressed air, process piping, ventilation for fumes, or clean room filtration. These systems must integrate seamlessly with structural and fire protection designs.
- Heavy-Duty Utility Infrastructure: Power, gas, water, and data demand can be extreme, especially in food processing, chemical production, or high-throughput logistics. Electrical service may exceed 4,000 amps, with separate systems for lighting, process loads, and backup generation. Switchgear and service rooms must be planned early.
- Logistics-First Site Planning: Site design revolves around truck circulation, loading docks, trailer storage, and intermodal access. Exterior slab grades, dock height, turning radii, and stormwater management are as critical as the building envelope.
- Regulatory and Safety Compliance: OSHA, EPA, FM Global, and industry-specific standards (e.g., USDA, GMP) govern industrial builds. This affects everything from aisle widths and signage to material finishes and spill containment.
- Design for Automation and Scalability: Facilities are increasingly outfitted with automation, from conveyor belts to robotic pickers. Structural support, IT routing, and slab flatness (FF/FL ratings) must be planned for long-term adaptability.
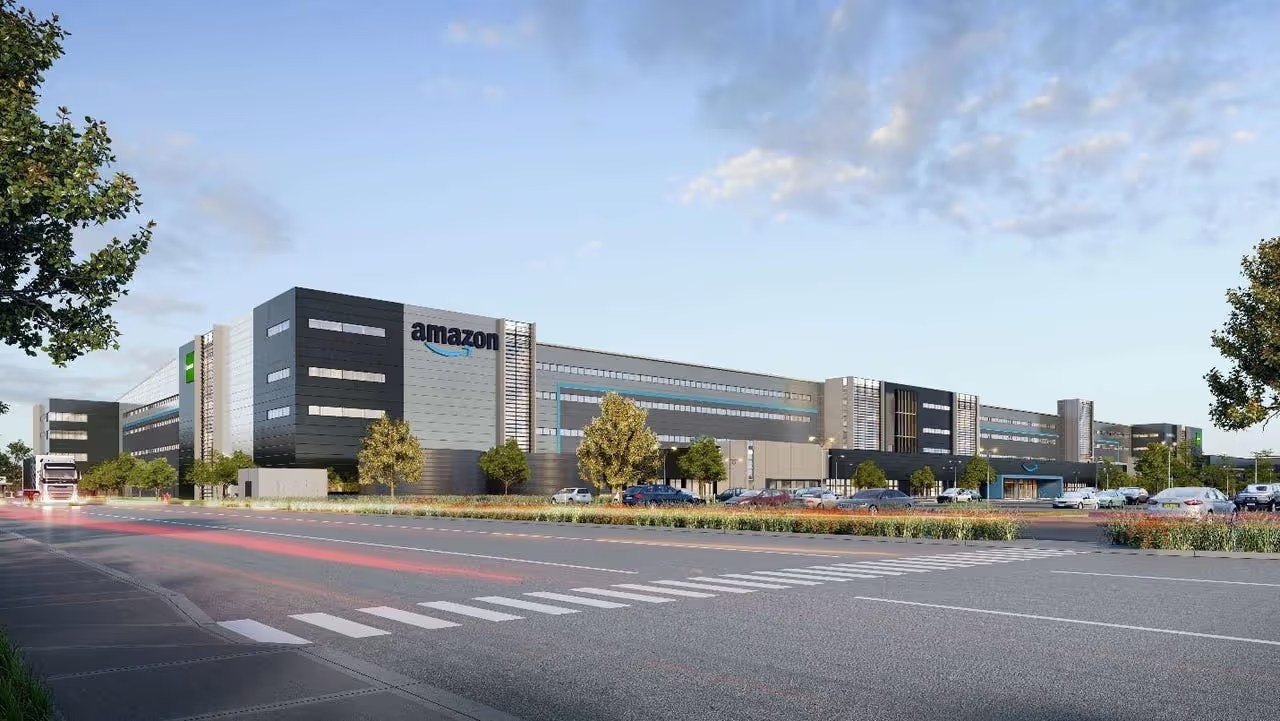
Example: Amazon Fulfillment Center, Kemps Creek (NSW)
At 200,000 sqm, this is Australia’s largest warehouse. The facility includes high-clearance racking, robotics integration, extensive dock planning, and sophisticated fire protection systems designed for automated logistics.
Final Thought on the Types of Commercial Construction
Commercial construction is about purpose-built environments. Each type of commercial construction, whether a hospital, a logistics hub, or a sports arena, demands a distinct construction approach. The systems, materials, sequencing, and compliance requirements change based on how the space will be used, who’s using it, and how often it needs to adapt.
For construction professionals, the real edge comes from understanding what you're building for. When you know the differences between commercial building types, you can deliver high-functioning assets that meet user needs, operator goals, and stakeholder expectations.